CNC Knee Mills

2 or 3 Axes Control | 3 Axes Readout | Powerful conversational CNC retrofit system for knee & bed mills
From the moment you power up your MILLPWRG2® system, you’ll know it was built with convenience in mind.
Large, full-color LCD display for exceptional clarity | Full 3D contouring capabilities | Menu-prompted conversational programming | Essential functions just a key stroke away | A full-function digital readout system or a programmable CNC control or both! | Powerful enough to handle any job | Easy enough for anyone to operate | No prior programming experience necessary
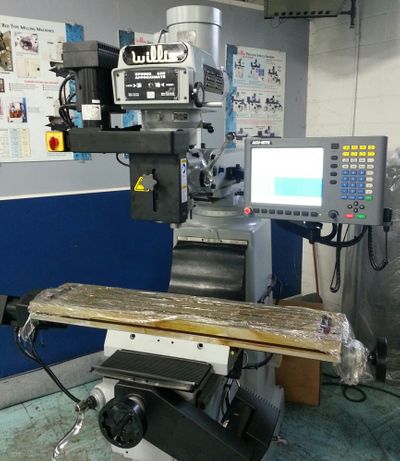
1050II
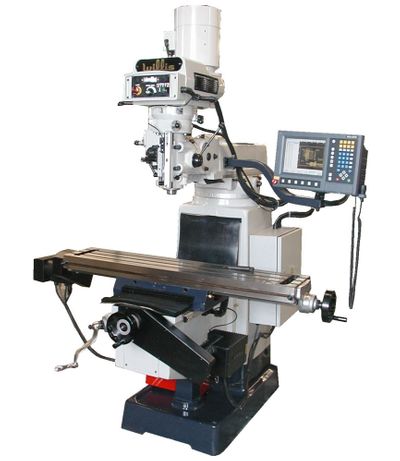
1050
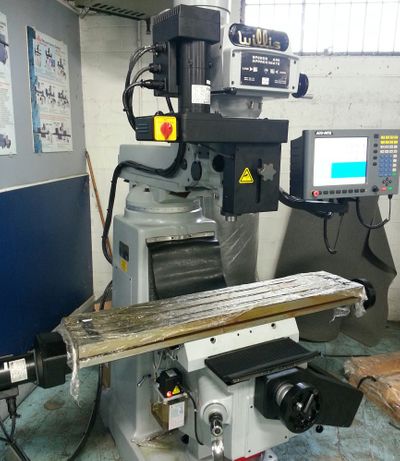
1050II
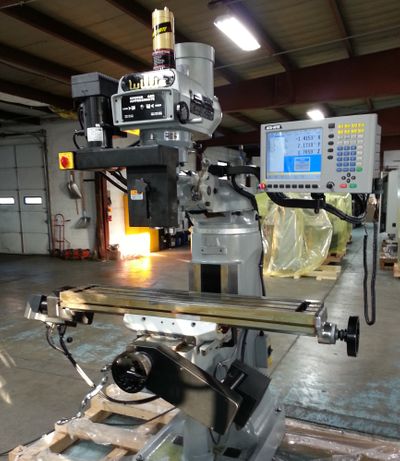
WM3VS
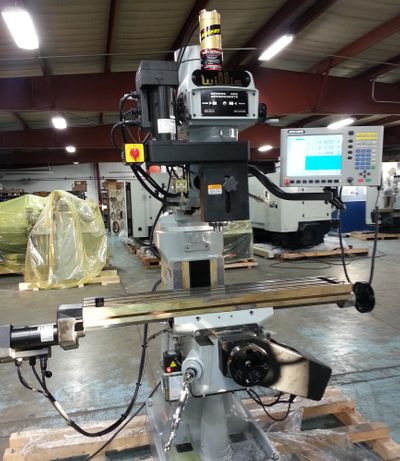
WM3VS
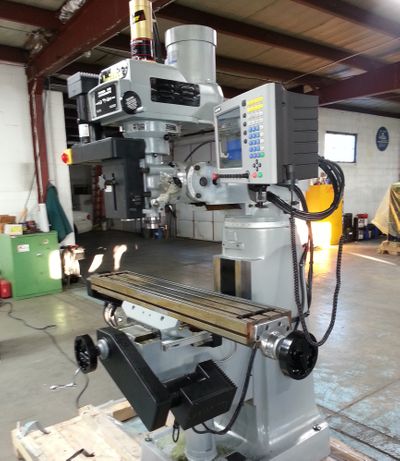
WM3VS
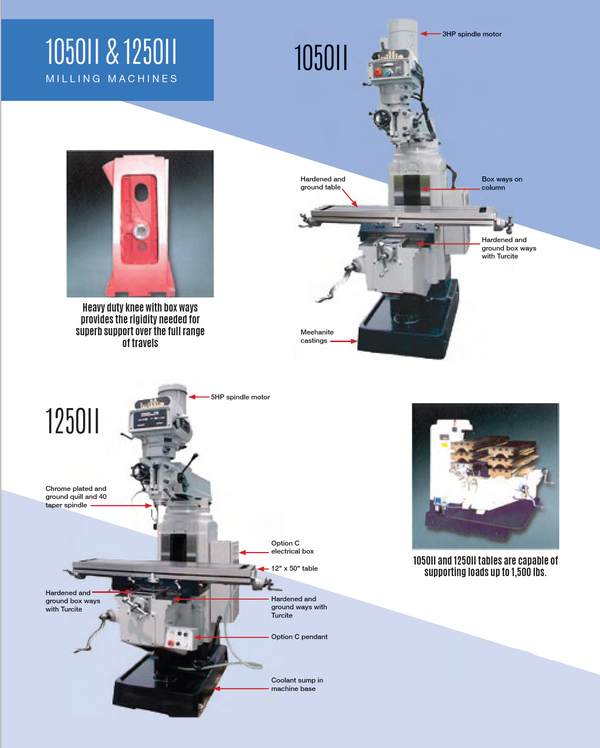
Click to zoom
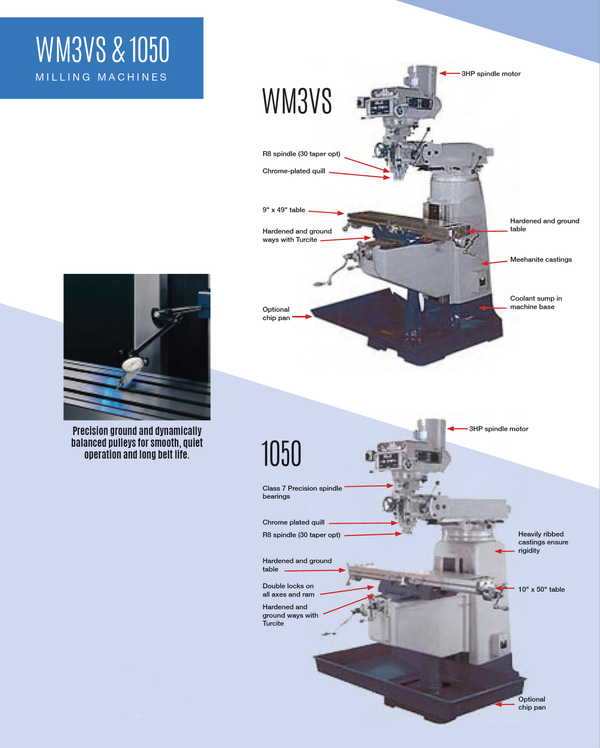
Click to zoom
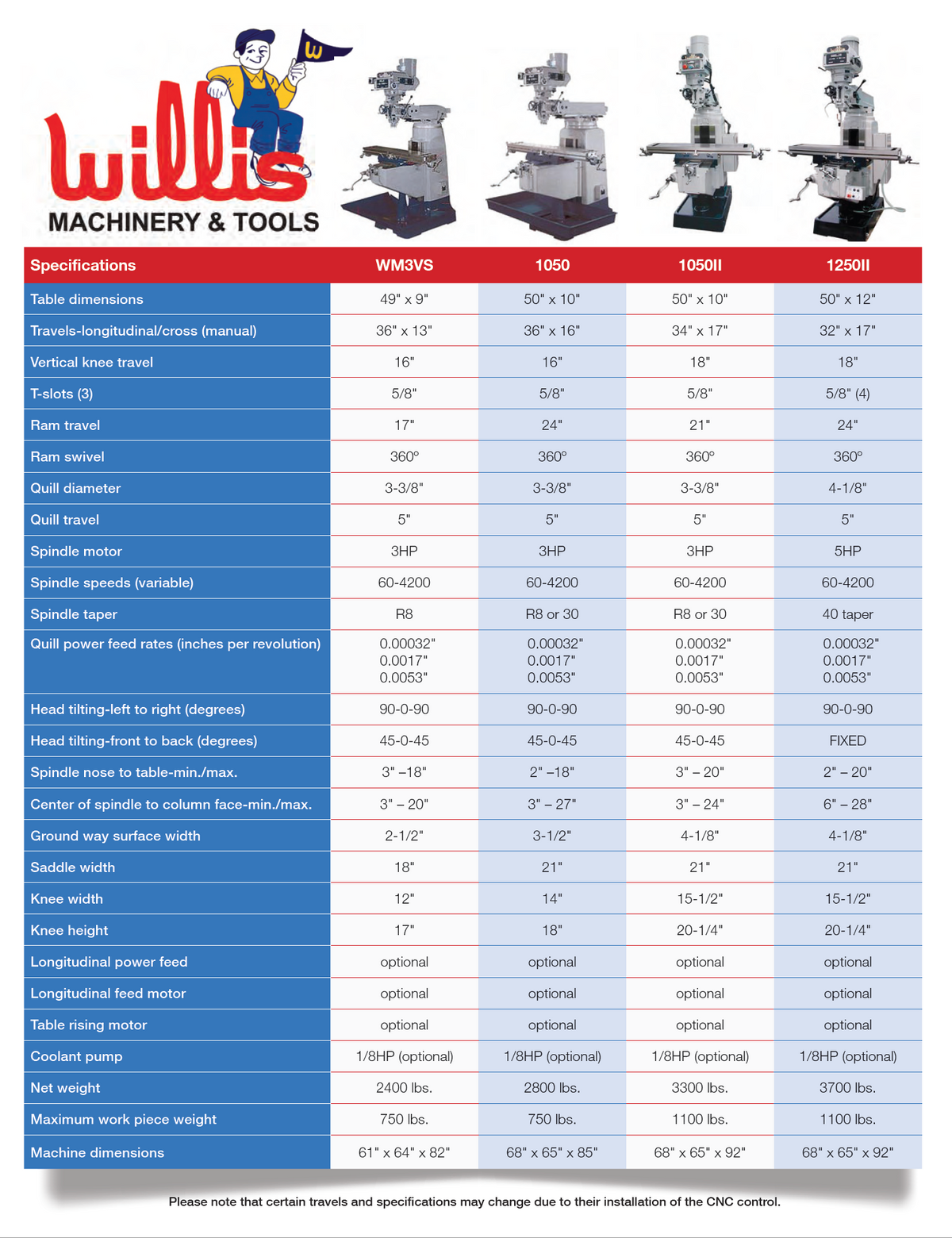
Inspection
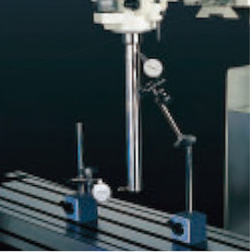
- Spindle Bore Runout
- Less than 0.0004"
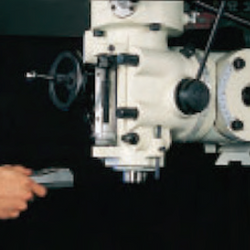
- Spindle Running Noise Measuring
- Less than 73 db at 1 meter
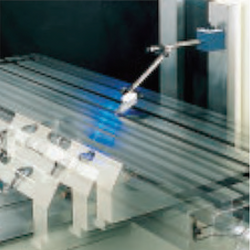
- Parallelism of Table Surface to Table Cross Travel Movement
- Less than 0.0008" per 12" of travel
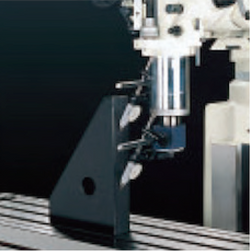
- Squareness of Table Surface to Quill Travel
- Less than 0.0008" per 5" of quill travel

- Squareness of Table Surface to Knee Travel
- Less than 0.0008" per 12" of travel
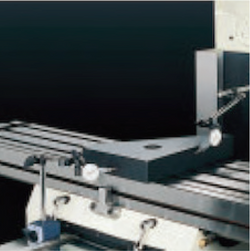
- Measuring of Squareness of Longitudinal Travel to Cross Travel
- Less than 0.0008" per 20" of travel
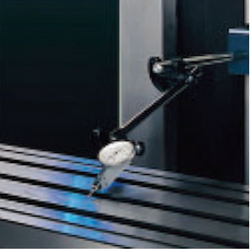
- Parallelism of Table Surface to Ram Cross Transverse Movement
- Less than 0.0008" per 12" of travel
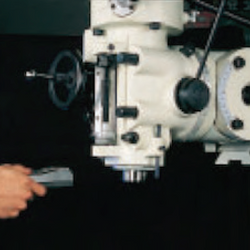
- Parallelism of Table Surface to Table
- Longitudinal Movement | Less than 0.0008" per 20" of travel
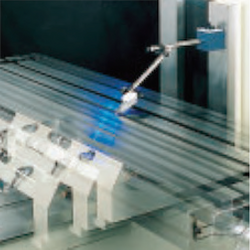
Stiffness of Head & Quill Combination